PILL GmbH – Vacuum etching technology has grown into the industry standard
The developer’s experience to the user’s benefit.
The electronics industry is subject to an extremely fast, dynamic development. nearly every day, we can see new achievements of electronics in trade offers. Across the years, the demands to the PCB industry have, however, continually grown. Higher time pressure in production, thinner PCBs, more and more delicate layouts pose great challenges to the PCB manufacturers. When PILL GmbH from Stuttgart presented its vacuum etching technology in the wet process about 15 years ago, it constituted a small revolution in PCB production. Now – 15 years later (!) – this technology has become a standard of PCB production.
Having developed a process for Pill wet-process systems early that has become a global trend in production technology is a special accolade. Plant constructor PILL GmbH from Auenwald has done it with its vacuum-etching-technology. New at the time, the technology relatively quickly became established on the market. It was a quantum leap in terms of precision and quality in the etching process. Driving results to unprecedented regions. The vacuum-etching-technology permits etching of the top and bottom of the PCBs in the same quality and highest precision in horizontal lines, dispensing with the elaborate and time-consuming post-etching pass.
The vacuum-etching-technology improved the etching-factor to 4. The etching flanks became much steeper, which benefitted refinement of the layout. Under-etching of the conductors was minimized.
Today – 15 years later –industry demand for the vacuum-procedure is still enormous. Of course, other providers are on the market as well who offer vacuum-etching-technology now. However, they cannot match the long experience of the PILL team. Who has the experience? Many customers consistently rely on the grown competence from Auenwald. The company has supported many customers across the years and has grown with them. communication and direct feedback have contributed a lot to the development and continuous improvement of technology. The success on the last specialist trade fair ‚Productronica‘ once again shows that new customers keep coming.
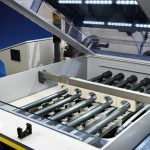
View into an alkaline vacuum-etching plant
The team of PILL GmbH focused on refinement and further development of the process introduced by it from the beginning. They profitably used the core competences for progress, which is also supported by the low employee fluctuation. The experience was collected in the company and has stayed there. The plant constructor from Southern Germany is represented in the electronic industry around the world. It is particularly strong in the German-speaking markets, but focuses on all of Europe. Russia is a stable market that PILL has been serving for many years. Good, completely trouble-free business partnerships in spite of the original crisis situation there characterize the relationships.
What makes long experience so special? While other providers on the market are still in the prototype phase or collecting experience, PILL supplies the latest developments of its own product. Interactive exchange with customers has made it possible to always adjust the vacuum model to the current needs. for example, there is barely any other system on the market in which PCBs with a film thickness from 50 µm to a panel thickness of 5 mm can be processed – without retrofitting and time loss.
The plant technology has been further development and optimized to perform the tasks even more precisely and to increase flexibility in use. Many systems, e.g. on the Asian market, lack these flexible options. In addition to the transport system, the nozzles have been developed. Angles and distances have been optimized to improve distribution of the etching fluid. This way, the etching edges are even more precise now. Different housings in PP and PVC designs are also available today.
Market requirements are growing. Developers of the PILL-team face this challenge and make the abilities of their plants grow along with the technical development – while also looking into the future. Apart from mechanical improvements to the plants, the developers are also working with different chemicals. Their system is suitable for acidic as well as alkaline processes. Great value has been put from the beginning on the plants being enclosed systems where the chemicals used remain within the production cycle without escaping. It is one of many environmental aspects that has always been part of development.
The use of different chemicals permits optimal adjustment to the customer’s specific materials to be processed in the system. Alkaline etching fluids are used for processing of metallic materials. Acidic ones are the rule in photoresist PCBs. The development team consistently focuses on the subject to wet processes to stay at the latest state of the art at all times.
The example from practice shows that it makes sense to focus on core competences. The company from Auenwald has set standards that are observed and applied.
The team does not worry that competitors try to place new plants in this area in its industry. If you want to learn about the experience and technical options, contact PILL GmbH in Auenwald. This is where experience is built.